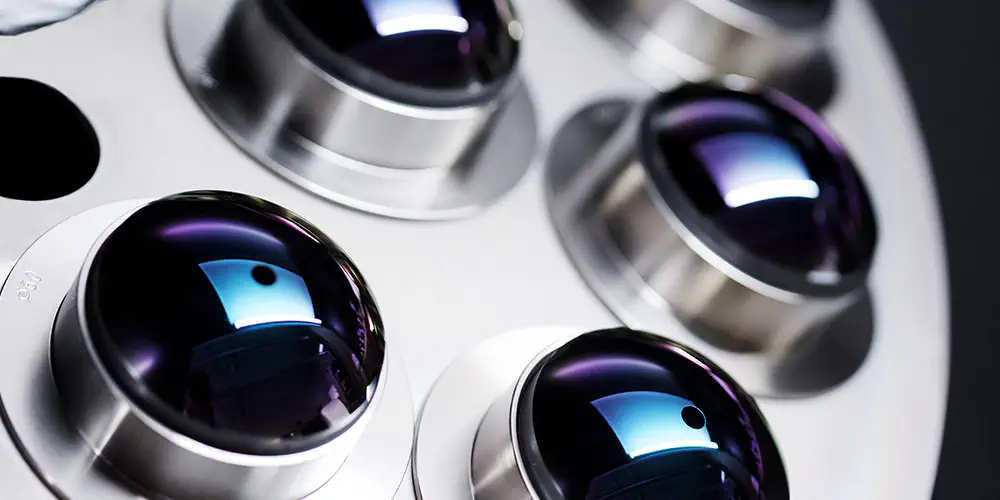
Coating technologies
State-of-the-art technologies for maximum precision
Electron beam evaporation, ion assisted deposition und magnetron sputtering
asphericons optics production offers various technologies for the optical coating process. The choice depends on the properties of the raw material and the specifications of the optical systems/products. Our experts will be happy to advise you on choosing the right technology for coating your optics and systems. The range of services includes:
- Electron beam evaporation
- Ion assisted deposition and
- Magnetron sputtering
Electron beam evaporation
Electron beam evaporation (EBE) is a process, in which optical components are coated in a vacuum chamber by evaporation of a material located at the bottom. The energy required for evaporation is generated by an electron beam. The vapor particles of the heated material propagate almost linearly in the vacuum. They condense evenly when they hit the surface of the optical substrate held at upper part of the evaporation chamber, which is located on a rotating calotte.
Specifications Electron beam evaporation:
- Coating: dielectric mirrors, anti-reflective and metal coatings
- Substrate size: up to a diameter of 300 mm
- Spectral range: 190 – 5100 nm
- Fast-Lane coating (24/48h delivery)
Electron beam evaporation process:
Figure 1: Schematic representation of the evaporation process
Ion Assisted Deposition
Ion Assisted Deposition is based on the electron beam evaporation process and used for most optical coatings at asphericon. In addition, a plasma source is used in this coating process to additionally densify the resulting layer by ion bombardment. The result is an even harder, more stable layer.
Specifications Ion Assisted Deposition:
- Coating: dielectric mirrors, anti-reflective coatings
- Substrate sizes: up to a diameter of 300 mm
- Spectral range: 190 - 5100 nm
- Very high coating hardness and stability
- Good thermal conductivity
- Fast-Lane coating (24/48h delivery)
Magnetron Sputtering
In magnetron sputtering, high-energy ions are generated in a vacuum from an AR plasma, which are directly pushed against a solid-state target. This is achieved by applying an electric field. As a result, ions and atoms are knocked out of the target and accelerated in the direction of the substrate by the electric field. The atoms and ions of the target are deposited on the top-mounted substrate (“sputter-up”) and thus form a high-quality and uniform optical coating. The layer growth can be monitored spectroscopically and thus ensures high process stability and reproducibility.
Specifications Magnetron Sputtering:
- Coating: dielectric mirrors, anti-reflective coatings
- Substrate sizes: 15 mm - 250 mm
- Materials: glass, quartz, crystals
- Spectral range: UV - NIR (380 - 5100 nm)
- Very dense and uniform coatings
- Higher sputter rates, separately loadable magazine sluices
Magnetron Sputtering process:
Figure 2: Schematic diagram of IBS