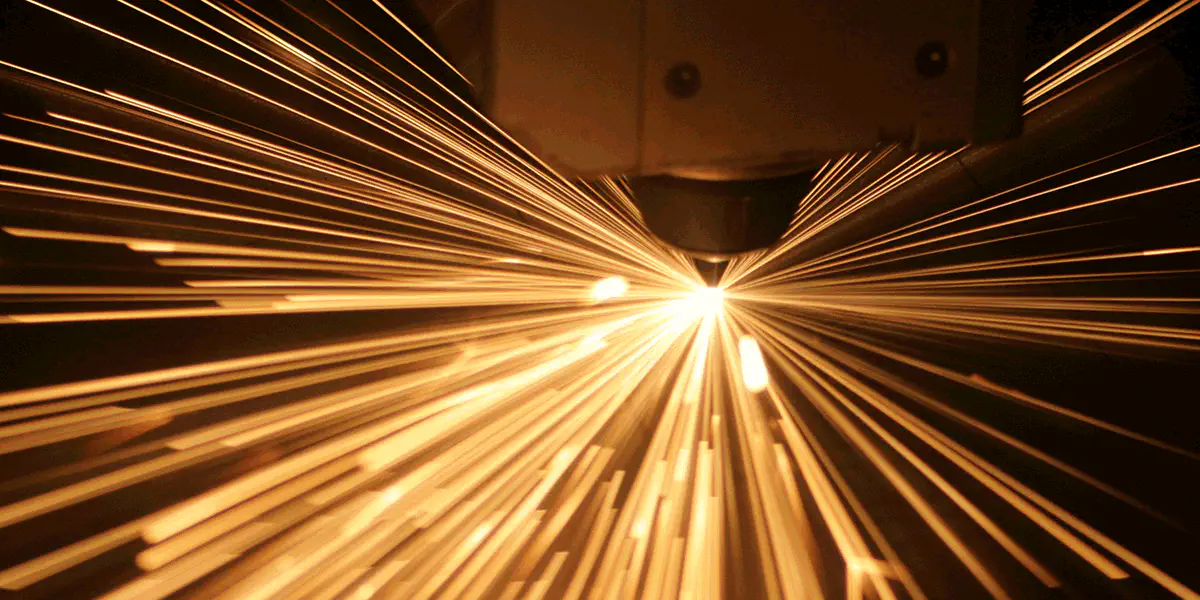
Beam shaping optics for laser welding
Reference project
Reduced production time, optimal welds
Additive manufacturing processes are increasingly being used for the production of complex components with a high degree of automation. Thanks to precise laser beam guidance, they enable a layered, flexible construction, e.g. of binomial structures. Hybrid processes combine conventionally manufactured structures with delicate structures created by additive manufacturing using laser welding. This type of production is used, for example, at the ifw Jena. In order to produce homogeneous welds, BeamTuning products for optimizing beam shaping were used in close cooperation with asphericon.
Project details
Additive manufacturing processes are an increasingly popular production method for complex components with a high degree of automation. Thanks to precise laser beam guidance, innovative additive processes such as powder bed-based melting enable flexible and exact, layer-by-layer structures to be made, for cooling channels or binomial structures for example. Only the time factor can be a limiting parameter, especially since the costs increase with longer production times. We are constantly looking for new optimization methods to reduce time and costs significantly. A new approach is hybrid manufacturing, which has been tested by the Günter Köhler Institute for Joining Technology and Materials Testing (Günter-Köhler-Institut für Fügetechnik und Werkstoffprüfung (ifw)) in Jena. In this process, less complex and conventionally manufactured structures are combined with complicated structures made with additive manufacturing using laser beam welding. In order to produce homogeneous welds of high quality, however, process parameters such as beam shaping in the focus area had to be optimized first.
Project realization
In close cooperation with asphericon, the ifw integrated various BeamTuning solutions (a|BeamExpander, a|AiryShape) into the existing system technology. This led to an improvement in process stability and reduction of spatter formation.
Figure 1: Schematic set-up of the optimized beam path with an a|AiryShape and an a|BeamExpander
In the set-up, the a|BeamExpander first enables the expansion of laser beams, while the a|AiryShape beam shaper, in combination with a focusing lens, converts the collimated Gaussian beams into various focused profiles (e.g. top hat, donut). As a result of the improved outgassing behavior, a pore-free, gas-tight weld seam can be produced. Safe melting of the seam flank prevents edge and root notches and thus provides a high-quality weld seam result.
Process results
Radiographic inspection of the weld seam:
Figure 2: Seam welded by Gaussian profile with pores (top), non-porous top-hat profile (bottom)
Seam cross-section of an LPBF-welded component:
Figure 3: Welded with Gaussian beam (left), top-hat (middle) and donut (right). The increase in process stability led to a homogeneous weld bead and expansion.
Optics for ifw at a glance:
- Integration of a|BeamExpander and a|AiryShape (creation of various focused profiles, e.g. top hat, donut) into existing system technology
- Improvement of process stability and outgassing behavior for the production of high-quality, pore-free, gas-tight welds (without edge/root notches)
- Reduction of spatter and production time
Learn more about the principle of our beam shaper a|AiryShape at: asphericon.com/en/solutions/products/beamtuning/beam-shaping/