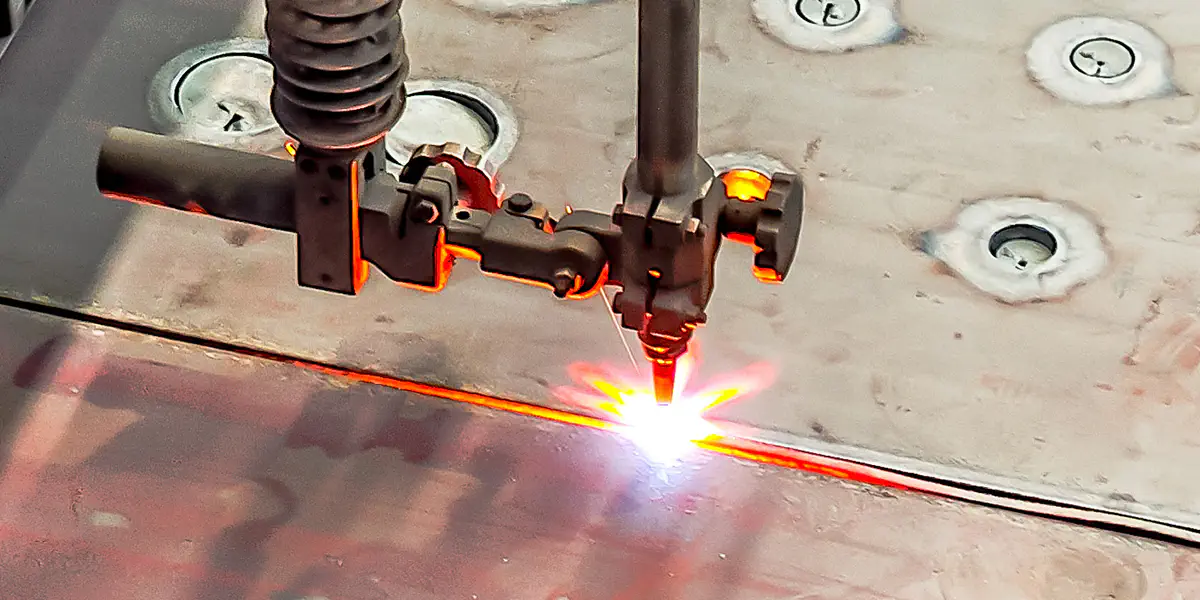
Laser Welding
Laser material processing for precise connections with a long service life
Laser welding is an industrial process for joining materials, e.g. metals or plastics. The laser heats a material to its melting temperature, so individual surfaces of a workpiece or different materials can be joined together by the resulting weld seam. Since the laser is moved relative to the workpiece, any weld seam guidance can be easily realized and flexibly adapted to a wide variety of workpiece geometries. High economic efficiency, little or no reworking and high speed make laser welding a basic technology in a wide variety of areas. Thanks to clean welds and high precision, the process is used, for example, in the manufacture of medical devices. High mechanical strength of laser-welded joints, high-pressure density and almost attainable basic material strength of laser-welded workpieces also make the process an indispensable joining process in the automotive, electronics, marine and household goods industries.
The principle of laser welding
In laser welding, also known as heat conduction welding, various lasers are used, e.g.CO2 lasers, solid-state lasers or diode lasers. All lasers have the principle of cutting in common: The emitted beam is focused via a special optical system onto a very small point on the workpiece to be processed. The workpiece lying directly under laser head is melted in the focus of the beam by high energy concentration of light and the joining starts. The resulting weld seam is extremely precise and leaves no residue whatsoever, such as microparticles. Due to the small focus of the laser beam, the weld seam cools down rapidly, so the thermal distortion of a workpiece is correspondingly low. The result is a narrow and extremely precise weld that requires little or no reworking. The controlled melt guarantees high-quality connections. Due to their high quality, weld seams are resistant to mechanical stress and have a long service life.
Deep penetration welding
In contrast to heat conduction welding, deep penetration welding involves drilling an additional hole in the workpiece to be processed. This is used for welding at a certain depth. If a workpiece is in the focus of the laser and the steam produced by irradiation flows off, the resulting melt is displaced by the resulting pressure. A narrow, vapor-filled hole is formed at this depth, the so-called vapor capillary (also called keyhole). When the laser is guided along the weld seam, this vapor capillary moves with it and is completely surrounded by molten metal. The laser beam causes reflections on the molten walls of the vapor capillary. This relates to the absorption of the beam by the melt. The result is an increase in efficiency. Due to movement of the laser, covered areas cool down and then solidify. The result is a deep weld seam of high quality. Deep penetration welding is mainly used for materials of high thickness.
Mirrors and beam shapers for exact transformation of laser beams
A high laser power and exact focusing of the laser beam are realized by high-quality optics. Special mirrors, high-precision lenses and compressed lens systems form the basic components for the creation of a powerful laser beam. Whether high reflectance, exact beam shaping and focusing or best image quality, our products promise consistently high performance, durability and effectiveness. The BeamTuning product range, for example, includes various laser beam shapers and expanders for transforming Gaussian laser beams into collimated and focused Top-Hat beams for various applications. Refinement of optical surfaces by high-end finishing processes can additionally perfect the results and ensure optimum results in laser welding.
Femtosecond optics
The use of ultrashort pulse lasers allows a direct transition of a material into gaseous state. Material removal is achieved by ultrashort pulses in the range of picoseconds to femtoseconds. A necessary condition is an optimal focusing of the laser beam on the material to be processed. The advantage regarding material processing arises from material-protecting properties of the pulses. Due to the direct transition to the gaseous state, non-desirable melting, changes in microstructure and thermal stresses within the workpiece can be reduced to a minimum.