High-performance optical coating
Optical coatings for demanding applications
Content
To further increase the performance of optical components such as mirrors and lenses they commonly are treated with an optical coating. The applied layers have various properties such as reduction of reflections (anti-reflection) for certain wavelengths. The amount, thickness and difference of the refractive indices (optical density) of each layer significantly influence the optical properties of a layered coating. However, an optical coating is not only used in professional optics or technology sectors, but also in everyday objects such as glasses, displays or on windowpanes.
In our two-part article series on this subject, we present various optical coatings with their fields of application as well as modern coating technologies. Learn more about selected coating options below. For more insight into methods of optical coating e.g., thermal deposition please see “Optical coating methods”.
What is an optical coating?
Coating refers to the process in which a material is applied as a thin, firmly adhering layer to a base material (substrate), for example glass. In the optical industry, dielectric materials and metals are primarily used for this purpose. An optical coating can change the properties of light passing through an optical component by selectively using the inherent properties of the materials used. This includes influencing the degree of reflection, transmission and polarization as well as the change in phase of the light.
Thin films with great effect – coating possibilities
The most common optical coatings are:
- Metal optical coating (mirrors, e.g. Al, Ag, Au)
- Dielectric coatings
- Anti-reflective coatings (AR)
- Beam splitter coating
- Optical filters
Reflective optical coatings
Due to the low mechanical and chemical resistance of the metal layers, it is beneficial to protect them with dielectric layers.
Figure 1: Coating curve for a protected and unprotected silver mirror
Dielectric optical coatings
Another type of coating for optics are dielectric coatings. They show very low absorption of incoming rays. Therefore, dielectric materials are often used for mirrors with particularly high reflectivity requirements. Likewise, the targeted wavelengths that are for example transmitted, can be tuned very precisely.
By using dielectric layer materials, it is possible to produce absorption-minimized mirrors that are used, for example, as deflection mirrors or pump mirrors in laser resonators. For certain wavelength ranges, these coatings achieve reflectivity greater than 99.9%. Dielectric mirrors are designed for specific angles of incidence and offer a stress-minimized and therefore durable solution for applications with maximum power.
Figure 2: Coating curve of wavelength dependent reflectance for a dielectric mirror
Antireflection coatings (AR)
Antireflection coatings are essential for maximizing the transmission of an optical system in many applications. A distinction can be made between single layer, broadband optical coating, or anti-reflective coating especially for laser applications. For the latter, coatings such as V-coatings are essential to protect the elements from damage. Depending on the glass used, a residual reflection of < 0.1% can be achieved. The main field of application of antireflection coating is to minimize reflection losses in the beam guidance of optical systems by the coating of all optical surfaces.
Broadband coatings in particular have a comprehensive range of applications. Optics with a broadband coating cover all common wavelengths in the NIR, UV range. The reflection is minimal in the intended wavelength range. When using super broadband coatings, large parts of the spectrum are only marginally reflected. This makes broadband coatings suitable for lasers of all types extending the lifetime of optical surfaces and enabling high power levels without requiring specific wavelengths. Even for specific wavelengths, such coatings can be a solution at the most efficient points of their reflection curves.
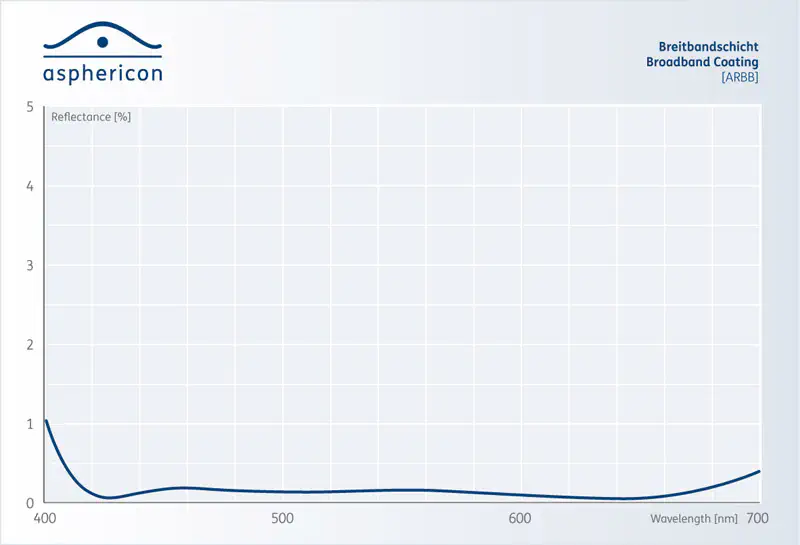
Figure 3: Exemplary coating curve for an anti-reflection broadband coating (ARBB)
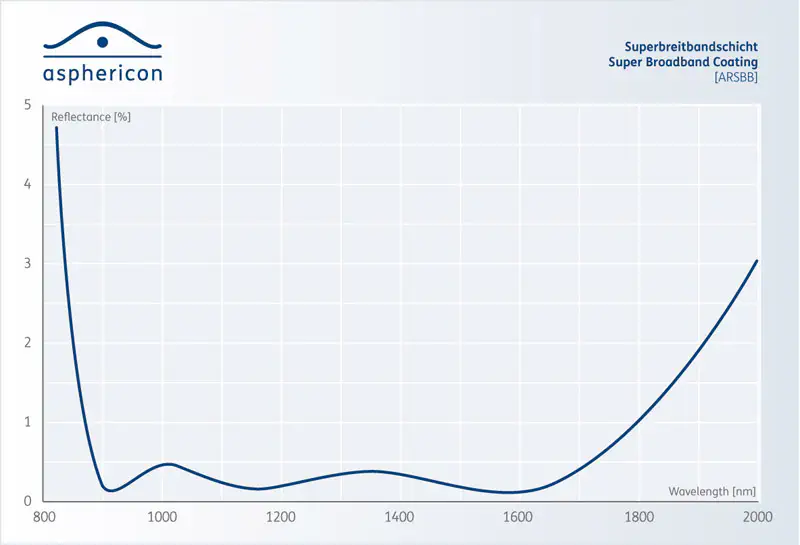
Figure 4: Exemplary coating curve for an antireflection super wide-band coating (ARSBB)
When light passes through the interface, part of the light is reflected, depending on the substrate and input material. This reflected light is no longer part of the transmitted light. The loss adds up with the number of interfaces in the optical system. To keep the losses as low as possible, the interfaces must be anti-reflective. Reducing the absorption of light leads to higher power limits of the optics and enables more powerful lasers for research and manufacturing. Reflected beams interfere with sensitive components of a system. Reducing radiation loss improves stability and enables more accurate measurements.
V-coatings are a special type of anti-reflection coating. A V-coating has maximum transmission for a very narrow range of light, while other wavelengths show significantly higher reflectivity. V-Coatings are reasonably priced to produce while achieving very good results. The reflectivity plotted by wavelength shows the V-shape that gives it its name. V-coatings are preferred for lasers with one wavelength since minimal reflections only occur at the intended wavelength. Due to the design, other wavelengths are strongly reflected. Therefore, V-coatings are only used when deviations from the intended wavelength are small.
Figure 5: Exemplary reflectance curve of a V-Coating for the wavelength 355 nm.
Coatings for beam splitters
Filter coatings
Filter coatings are used in many different industrial applications, e. g. in fluorescence microscopy. TThis type of optical coating is used to transmit, reflect, absorb or attenuate light of specific wavelengths.
The defining property of filter coatings is a high transmission for specified wavelengths, while other wavelengths have very low transmission. For example, an edge filter transmits rays below a defined length while longer wavelengths are reflected or absorbed. The reflectivity shows an “edge” in the graph, above which wavelength is (no longer) transmitted. In addition to edge filters, just single wavelengths can be transmitted, here V-coating is a representative.
The use of dielectric layers on glass enables, among other things, the separation of different wavelengths as short-pass or long-pass filters. Short-pass filters transmit short wavelengths, while long wavelengths are reflected. Long-pass filters, on the other hand, only transmit long wavelengths and reflect the short ones. Filter coatings are used, for example, in eyeglass lenses (UV radiation is blocked while visual light is transmitted) and in rangefinders (visual light is blocked while infrared light is transmitted).
Figure 6: Exemplary reflectance for a long-pass filter (LPF)
Depending on the properties of the materials and the requirements of the optical systems different processes are used to apply the presented optical coatings. We address the coating technologies in a separate blog post.